

The job should be held in the vice in such a way that its cutting lines are clearly visible.While fixing the blade on the frame it should be ensured that its teeth should cut the metal when they are driven forward.Selection of hacksaw blade should be done according to the metal for which it is to be used.Methods of Using Hacksawįor the efficient cutting the following points should be borne in mind: This type of setting is done on blades of fine grade and superfine grades. In this type of setting a few teeth are bent to the right and a few to the left.
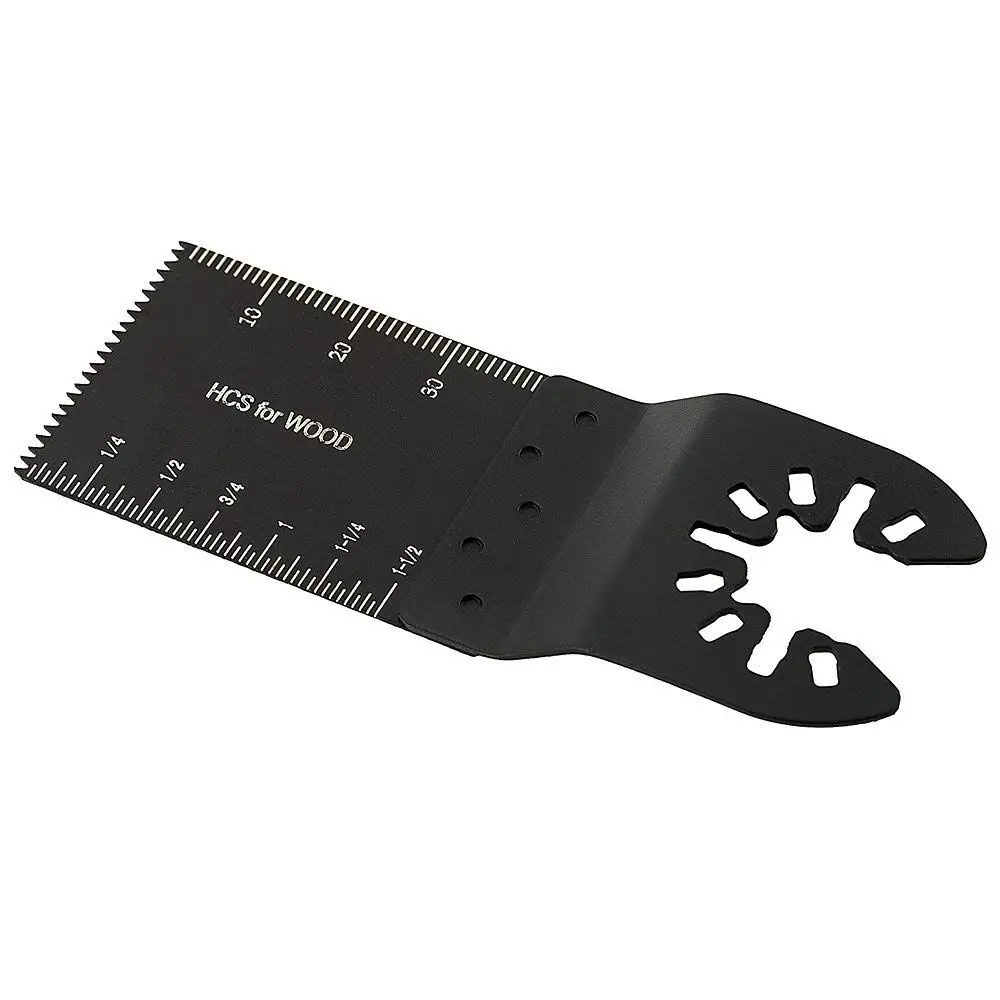
In this type of setting, two teeth are turned to the right and two to the left and one dent between them is left straight, which performs the function of clearing the metal particles from the slot. This type of setting has been shown in fig. This tooth helps in cleaning the metal particles from the slot. In this type of setting, one tooth is bent to the left and the next tooth to the right and every fifth tooth is kept straight. The setting of teeth in a blade is done in three ways. If the setting is not done, there is a great risk that the blade would get stuck in the metal and get broken. Go with a blade with a curved design for easy push and pull cutting.Therefore, because of this slot, the blade does not get stuck while operating it.
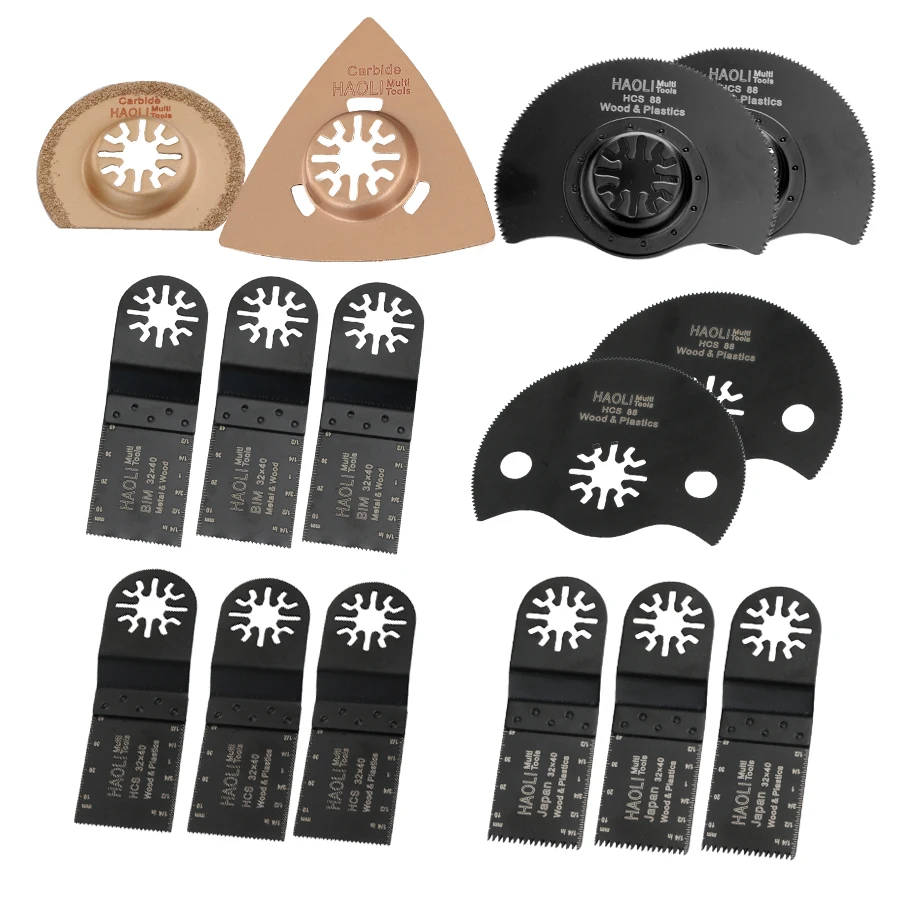
Keep in mind, the coarser the sandpaper, the rougher the sanded surface will be. The triangular-shaped sanding head or pad smooths rough wood in corners and will level uneven surfaces of wood or paint. Try a flexible scraper blade or triangular-shaped head with mating coarse-grit sanding pads. More specifically, consider a segment blade shape for working in corners and on edges without overcutting. Select a grinder blade for this tough task. Pointed design for grinding and rasping in tight corners Look for a blade with the following attributes: carbide-coated edge,Ĭoarse carbide-grit bottom for aggressive material removal over large surface areas, and a Another consideration is a triangular-shaped blade with pointed ends for grinding and rasping in tight corners Some blades come in 1/16” and 1/8” thicknesses to match grout widths. A diamond-coated blade saves you money as it lasts two to three times as long. Consider a blade with a Japanese tooth design for fast, clean, and precise cuts.įor small jobs, consider a carbide blade, and for larger jobs, try a diamond-coated blade. Your first choice should be a flush-cutting blade. It isn’t as fast as a wood-cutting blade, but it won’t be destroyed by hitting a hidden nail or screw. If there’s a chance, you’ll hit metal when cutting wood, used a bi-metal blade. Go with a straight cutting blade for push cuts or a multi-knife blade featuring a push/pull hooked design for fast, clean, controlled cuts The smaller-toothed blade cuts well, but can easily clog. A large-toothed blade cuts faster than a fine-toothed blade. One right choice is a chrome vanadium blade featuring a Japanese-style tooth design with a double row of alternating teeth. If the cut edges will be visible, a clean-cut is a must. When fine cuts are necessary, consider a blade with a Japanese tooth design for fast, clean, and precise cuts. The same blade used to cut carpet (above) can also be used for shingles.įor thicker metals, consider a hybrid blade like a titanium-coated model with carbide-embedded teeth for longer life. For more precise cuts, consider a bi-metal blade.Ī circular or semi-circular blade works well for cutting both sheet metal and plastics that might be prone to vibrating when cutting. Perfect for cutting openings for electrical boxes and recessed lighting, a bimetal or carbide-grit blade will cut the drywall and cut through a drywall nail or screw without dulling the blade.įor most plastic-cutting applications, a standard wood-cutting blade will suffice. Some blades come with a wavy tooth pattern to reduce strain on individual teeth for a superior cut. Select a bi-metal blade for this application. Non-Ferrous Metal (does not contain Iron): Make sure to choose a bi-metal blade manufactured explicitly for cutting metals or a combination of wood and metal. Cutting metal with a blade created for cutting wood will dull the edge quickly. Some blades are designed with a special push/pull hooked design for fast, clean, controlled cuts.Ī bi-metal and a fine-toothed blade look similar. Go with a scraper blade with a rounded convex edge. The diamond coating provides a long-lasting and consistent cut. To cut concrete, brick, plaster, grout, or other porous materials, check out a diamond or carbide-grit blade. This is a tough job, so go with a carbide-grit grout removal disk or blade. An excellent choice is a rectangular-shaped blade with opposing precision-ground cutting edges. Some scraper blades are flexible and ideal for scraping light material.
